
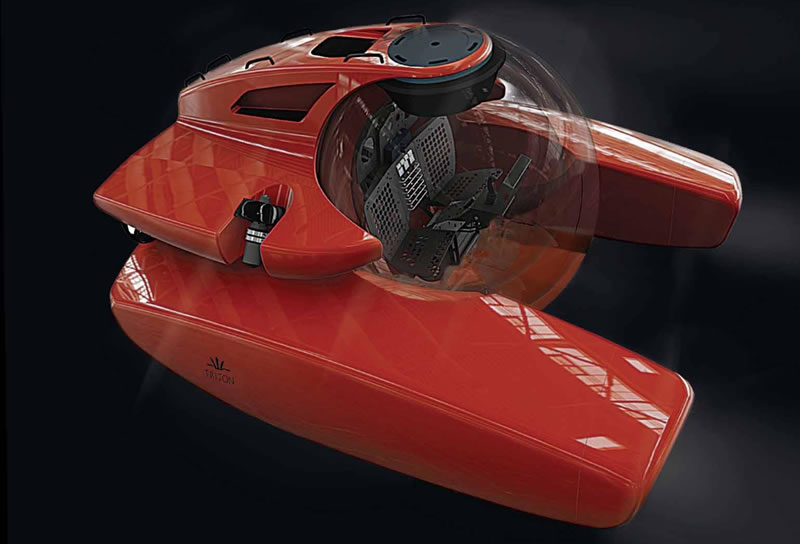
We would work in pairs, and one diver would position the pipe or valve while the other would connect it using nuts and bolts. The first was using a 500-pound lift bag to move a large bit of pipe onto a stand, and then attach a gate valve to this pipe. While wearing the Descos we worked on two projects that simulated jobs we could encounter in a real Hazmat environment. The diver also must go through a rigorous decontamination process before they can doff this equipment after a dive. Typically, the helmet will also be mated directly to the diver’s drysuit, which will contain gloves and boots, and will be methodically checked for cuts or cracks before and after a dive. This means that nothing on the outside of the helmet gets in, which is highly desirable when one is diving in contaminants. What this “free flow” does is create a higher pressure of air inside your helmet than the ambient pressure of the water (or whatever it may be you’re diving in). There’s a screw valve on the side of the hat that allows the diver to control the force of the flow of air, but there will always be air flowing, unless you dial the valve all the way closed. The redeeming feature of the Desco is that it provides the diver with a constant “free flow” of air. This involved diving in a helmet known as a Desco, which literally feels like you’re wearing a small television on your head (it’s huge and heavy, not molded to one’s head like many of the other dive helmets). However, only a small portion of the work occurred below the water, which is a reminder that even though we are all “divers,” a ton of what we do occurs “topside.” The wreck of the Davy Crockett Davy Crockett salvage operationĪfter completing the classroom portion of the HazMat course, we went back down to DIT’s Barge 8 to do the in-water portion of Diver in a Desco Pot Removing this wreck from the river was a massive operation, and nearly every worker involved was a commercial diver. One case study we did was on the salvage of the Davy Crockett, on the Columbia River in Washington State. In addition, many salvage projects involve diving in waters that have chemicals mixed in from damaged vessels. This can be due to cleaning up from oil spills, doing work in the foul waterways around New York City (what I want to do), or completing maintenance tasks on nuclear power plants, sewage treatment plants, or even animal processing plants. It’s very common for commercial divers to be exposed to hazardous materials. I got to try on a surface Hazmat suit during our training While five straight days of desk time was brutal for our class to endure, there were a lot of useful topics that we covered, which no doubt will help keep us out of harm’s way when we enter the workforce. The first part of this training was 40 hours of classroom time, which was mandatory in order to earn our HAZWOPER certification. After finishing our offshore module we went on to hazardous materials training. The past month of training has been really challenging and interesting.
